低压铸铝是一种在较低压力作用下完成铝合金液体充填铸铝模具型腔及凝固过程的铸造方法。低压铸铝因其独特的优点,在工业生产中得到了广泛应用。那么下面,
麻将胡了pg电子网站-pg电子官方网小编说一说关于低压铸铝生产过程中产品开裂的原因是多方面的,主要包括以下几个方面:
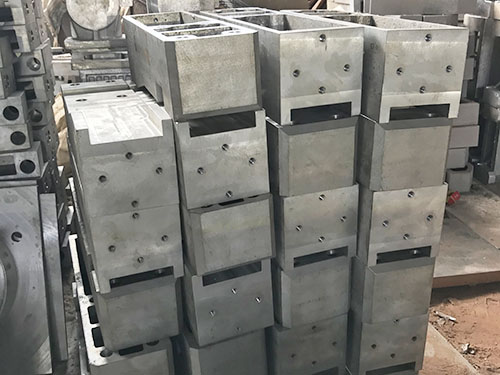
一、铸件结构设计因素
结构设计不当:轮毂或其他铸件的内圆角大小不当,是产生热裂纹普遍的原因。因为轮毂在冷却时尖角处会产生很大的应力,在内圆角小的部位,即使补缩良好不出现缩裂,也会产生热裂。此外,轮毂截面骤然改变,会导致冷却速度快慢不一,即使补缩良好也会产生较大应力,使轮毂凝固后出现裂口或裂纹。
二、工艺参数因素
保压时间过长:在低压铸造中,如果保压时间过长,可能导致升液管内液体出现凝固,在轮毂铸件顶出时承受一定的拉力,从而造成轮毂产生冷裂。
升液系统问题:升液管过长或设计不合理也可能导致类似问题。升液系统是指浇注时液态金属由坩埚进入型腔的通道,包括升液管、保温套和铸件浇注系统。设计合理的升液系统对减少裂纹倾向具有十分重要的意义。
三、模具温度因素
模具温度过低:模具温度决定合金液的凝固方式,并直接影响铸件的内部和表面状况。如果模具温度过低,铸件在金属型中冷却过快,铸件各部分之间的凝固速度不同,会使铸模内铸件的冷却不均匀,产生热应力和变形,结果导致在铸件成品上产生热裂及较大的残余应力和残余变形。
模具温度过高:虽然提高模具温度有利于应力的减小,但过高的模具温度也不利于得到结晶细小的组织,液态金属容易吸气和收缩,使铸件产生气孔、缩松和缩孔等缺陷的机会增加。
四、材料因素
铝中杂质含量不合理:工业纯铝中常含有铁与硅等杂质,这些杂质影响铝的可塑性。大量实验分析证实,硅铁杂质含量比对裂纹的影响很大,当硅铁比小于1.5或大于10时,均不出现裂纹,硅铁比在1.5~10之间易出现裂纹。
五、操作因素
操作不当:加工时未注意工件的正确定位、未及时更换刀具、过快的切削速度等,都可能导致压铸铝件的表面出现裂纹。此外,加工时过于强度过大,也可能使压铸铝件局部塑性变形,从而出现缺陷。
六、环境因素
环境温度:在较低温度下对材料进行加工,容易使材料过于脆性,增加开裂的风险。